Expert Welding Inspection Milwaukee Providers for Quality Assurance
How Welding Assessment Adds to Durability and Dependability in Construction Tasks
Welding assessment functions as a foundational element in guaranteeing the durability and reliability of construction projects. By systematically recognizing prospective problems during different phases of manufacturing, welding evaluations not just protect against expensive failures yet likewise cultivate a society of quality control within the team. Employing innovative strategies, such as non-destructive testing, promotes detailed examinations while preserving product honesty. As tasks advance, the influence of these evaluations comes to be progressively apparent, elevating vital inquiries regarding their lasting advantages and implications for total project success. What certain practices can be applied to make best use of these advantages?

Significance of Welding Assessment
Guaranteeing high quality through welding assessment is an essential part of any type of fabrication job. It acts as a secure to confirm that welding procedures satisfy well established criteria and specifications, thus enhancing the general stability of the structure or part being made. Welding inspection is not just a step-by-step action; it is a necessary practice that aids recognize prospective problems early, making certain that they are resolved prior to they intensify into substantial troubles.
The value of welding assessment can be highlighted by its duty in maintaining safety and security and longevity. Bonded joints are typically based on severe conditions, and any issues can jeopardize the efficiency and long life of the end product. By applying rigorous evaluation methods, companies can ensure conformity with market regulations, therefore reducing risks related to structural failings.
Furthermore, reliable welding evaluation fosters confidence among stakeholders, consisting of clients and regulatory bodies, that the project satisfies the finest standards. This not only boosts the reputation of the maker yet also contributes to long-lasting expense savings by avoiding rework and possible liabilities. Eventually, welding assessment is indispensable to the success and dependability of construction projects, reinforcing the worth of top quality assurance in engineering practices.
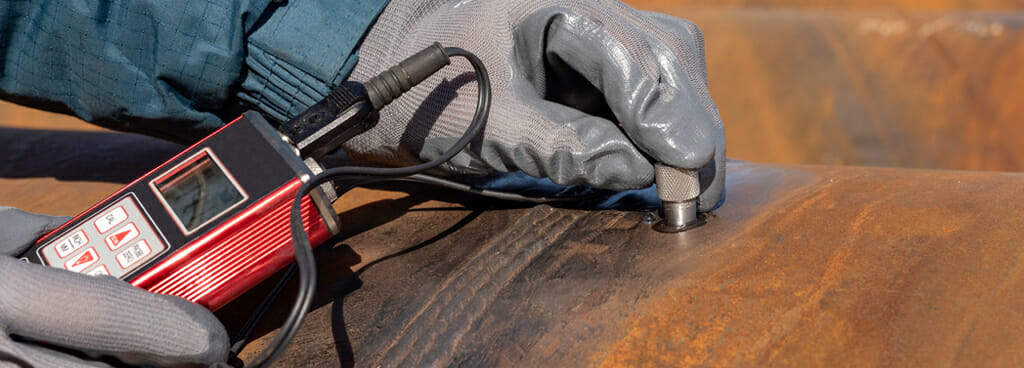
Common Welding Flaws
Welding defects can considerably undermine the architectural stability of produced components, making their identification and correction essential. Typical welding problems can be extensively categorized into three kinds: geometric, metallurgical, and service-related.
Geometric defects consist of concerns such as undercutting, where the base steel is worn down at the edge of the weld, and excessive convexity, which can lead to stress and anxiety focus points. These problems can jeopardize the toughness and sturdiness of the weld joint.
Metallurgical problems arise from improper welding treatments or products, resulting in issues such as porosity, where gas pockets create within the weld, and absence of fusion, which takes place when the weld steel stops working to bond correctly with the base steel. These problems can considerably damage the weld's effectiveness.
Service-related issues may not emerge until after the part remains in usage. Instances consist of cracking as a result of thermal stress and anxiety or exhaustion, which can bring about disastrous failures otherwise dealt with.
Understanding these typical defects encourages fabricators to apply effective inspection techniques that boost the reliability and long life of their jobs, inevitably making sure safety and security and performance requirements are met.
Assessment Approaches and techniques
A detailed strategy to assessment techniques and techniques is crucial for alleviating and identifying welding problems in manufacture tasks. Various techniques are employed to guarantee the stability of welds, consisting of aesthetic assessment, ultrasonic screening (UT), radiographic screening (RT), magnetic fragment screening (MT), and color penetrant testing (PT) Each method has its staminas and certain applications.
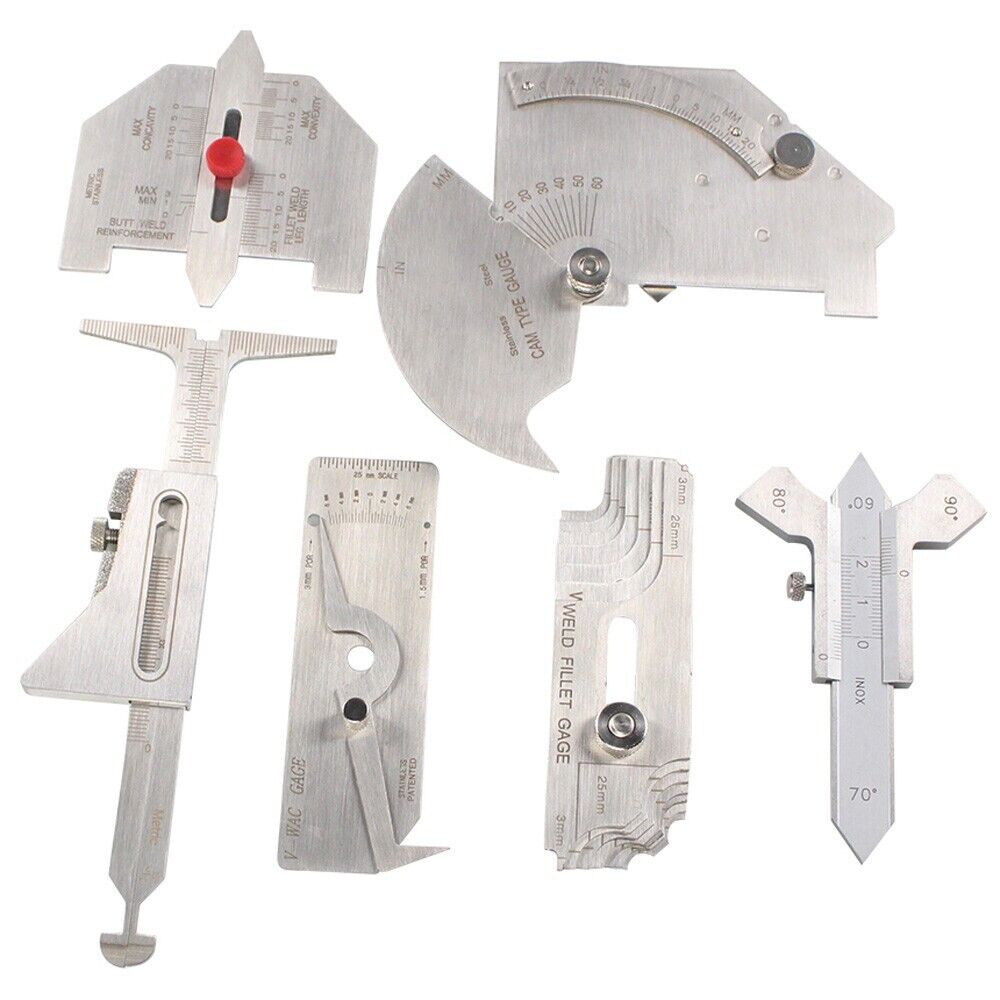
Magnetic bit testing is helpful for spotting surface area and near-surface issues in ferromagnetic materials. By using an electromagnetic field and utilizing ferrous bits, examiners can recognize interruptions efficiently. Color penetrant testing highlights surface-breaking problems with the application of a color that seeps into fractures, making them noticeable under ultraviolet light.
Using a combination of these techniques ensures an extensive evaluation, boosting the reliability of welded structures.
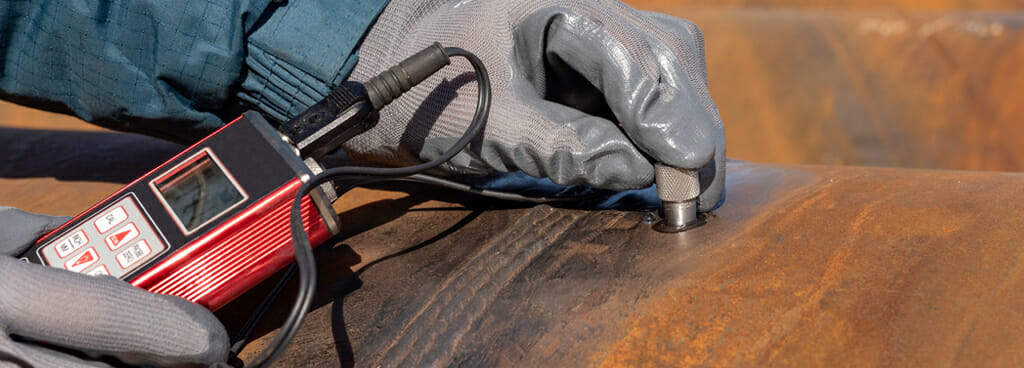
Effect On Project Longevity
Effective assessment methods substantially influence the durability of fabrication projects. By identifying potential issues and incongruities in welding procedures, examinations make certain that frameworks are constructed to stand up to operational stresses in time. When welds are thoroughly examined, the chance of unnoticed concerns, which can cause structural failings, is lessened.
Regular inspections facilitate adherence to sector requirements and regulations, which are essential for guaranteeing the sturdiness of bonded joints. Such conformity not just improves the integrity of the task however additionally guarantees stakeholders regarding the high quality of the work. Timely discovery of defects permits for corrective actions to be taken early, preventing pricey repair work or total overhauls down the line. Welding Inspection Milwaukee.
Additionally, efficient examination techniques foster a society of quality guarantee within fabrication teams. They are a lot more likely to stick to finest practices and maintain high requirements throughout the production process when employees are mindful that their job will certainly be rigorously evaluated. Ultimately, this dedication to quality not just extends the life-span of the job but likewise minimizes maintenance costs, therefore boosting the general economic feasibility of construction ventures.
Enhancing Integrity in Fabrication
Reliability in fabrication is substantially improved with extensive inspection procedures that attend to prospective weak points in welding practices. Efficient welding examination not just determines defects early however also supplies important comments to welders, guaranteeing adherence to established standards and specs. By making use of non-destructive testing techniques, such as ultrasonic or radiographic evaluations, makers can ascertain the honesty of welds without jeopardizing the product.
Additionally, routine evaluations cultivate a culture of quality and accountability amongst construction groups. When welders recognize that their work is subject to strict examinations, they are a lot more likely to abide by ideal practices and procedures. This proactive method minimizes the danger of costly failings during the functional stage of a job.
Inevitably, enhancing reliability in fabrication through detailed evaluation processes not only raises the life-span of the fabricated components but likewise reinforces stakeholder confidence in the job's overall quality and toughness. Investing in durable welding evaluation practices is essential for attaining long-lasting integrity in any fabrication undertaking.
Conclusion
In recap, welding inspection offers as an essential component in visit the website making sure the long life and integrity of fabrication projects. Inevitably, efficient welding examination techniques reinforce stakeholder self-confidence and dramatically contribute to the economic stability of construction ventures.
Welding inspection offers as a foundational component in guaranteeing the durability and reliability of manufacture jobs.Making certain quality through welding assessment is a crucial component of any type of manufacture task. Inevitably, welding evaluation is essential to the success and useful site dependability of fabrication projects, enhancing the worth of top quality assurance in design techniques.
A thorough approach to inspection techniques and methods is crucial for mitigating and recognizing welding problems in construction jobs.In summary, welding evaluation serves as a vital part in ensuring the longevity and integrity of manufacture tasks.